The tiny robots start out flat, thin wafers of layered silicon, gold and plastic.
It’s the heat created by an electric current that makes them fold along etched grooves, bending themselves into grippers, tiny boxes, even bee-sized origami cranes, moving in more complex ways that most microscale robots.
This is engineering inspired by origami, the Japanese art of paper folding, and the potential applications, according to University of Michigan engineering professor Evgueni Filipov, run a gamut from plumbing to high tech surveillance.
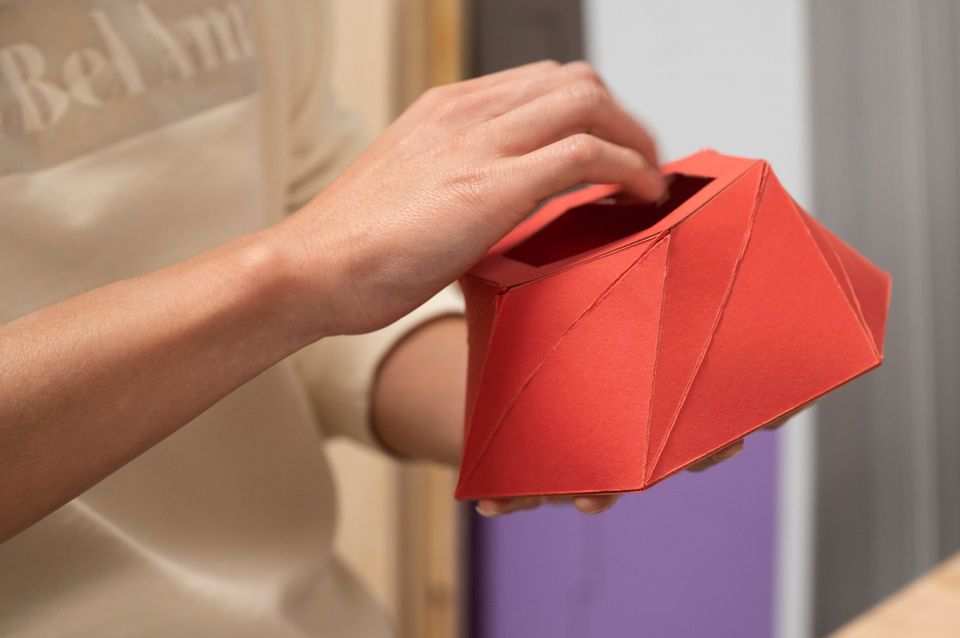
“You can have these microscale robotics for sensing, so maybe if you have a leak in your pipes, you flush it down your drain and it will go find out find where the leak is happening,” said Filipov, a civil engineer by training. “You could have reconnaissance micro drones.”
Or machines you could swallow to help find an ulcer, machines that could inspect hard-to-reach places on the inside of buildings, machines that could be mobilized for material testing at a mass scale.
They’re not there yet. But Filipov and his collaborators have developed a more efficient way to manufacture tiny three-dimensional robots. And that comes from origami.
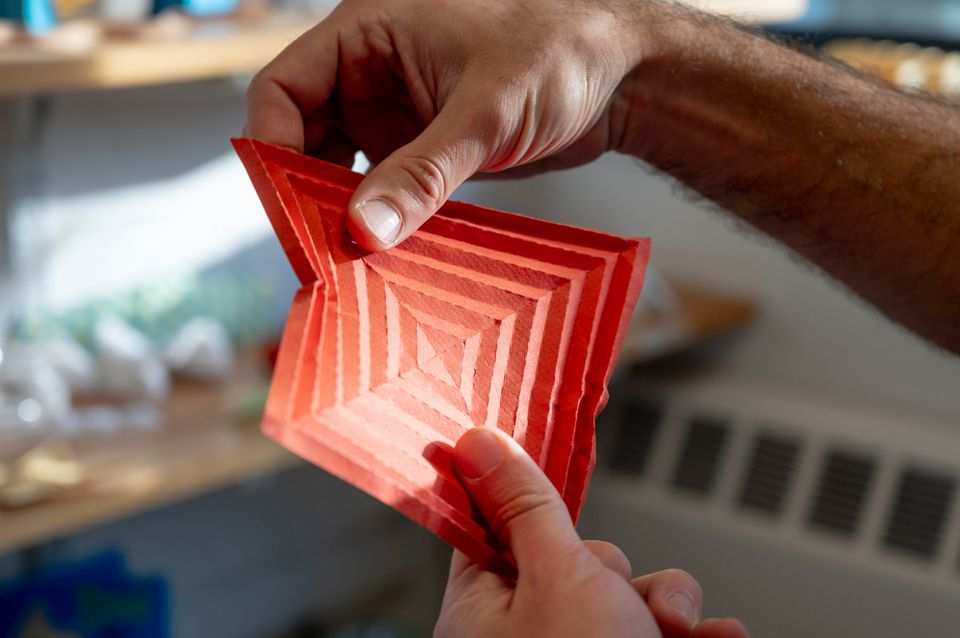
Origami is the Japanese art of paper folding, though it likely has its roots in China, where paper was invented in the early second century. The practice of paper folding spread in Japan hundreds of years later, first as part of Shinto religious ritual and later as an art form.
Origami’s most important rules in its modern iteration are no cutting and no glue.
Engineers and mathematicians eventually began to take an interest. They were holding conferences on the science of origami by the late 1980s.
But a program created a decade ago by the Air Force Research Laboratory and the National Science Foundation, dubbed the Origami Design for Integration of Self-assembling Systems for Engineering Innovation, kickstarted origami research in the U.S.
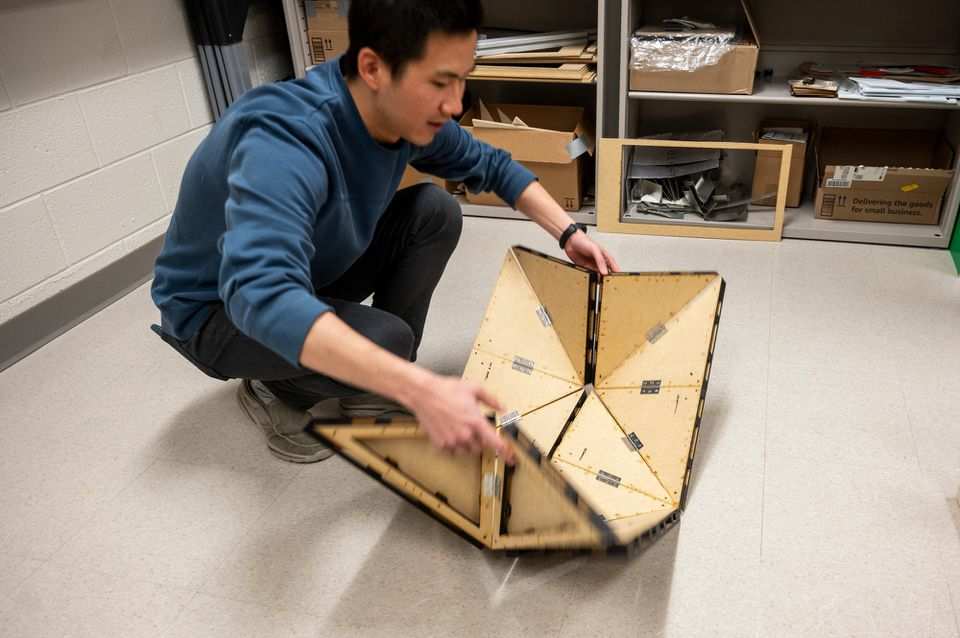
“Origami has become much more sophisticated,” said Larry Howell, a mechanical engineering professor at Brigham Young University whose lab has used principles of origami to design folding solar arrays for spacecraft, quick-deploying bullet proof barriers, even medical devices, “and what we noticed was [origami artists] were able to accomplish and get certain kinds of motions that we wouldn’t have been able to do with our traditional engineering approaches.”
Filipov came to origami-based engineering as a graduate student in civil engineering after realizing that the methods he was using to study how buildings and bridges behave during earthquakes were also useful for understanding origami-based structures.
“What it allows us to do is look at the structure from an outside perspective and understand where is it stiff, why is it stiff or why is it flexible?” he said.
Other work in his lab focuses on the ways in which bending and folding can add strength and stiffness to flat surfaces.
“This is called the origami hyperbolic paraboloid,” he said, holding a piece of paper that was both folded into ridges and bent in the middle like a butterfly rendered in odd geometry. “When you take a piece of paper, typically, it’s very difficult to form surfaces like this.”
But, when you do, the result is a structure that holds its shape in more than one position.
“Imagine you have something that you want to deploy and then retract and you want it to stay stable both in that retracted state and then when you pull it back and you don’t want it to kind of move a lot in between those,” he said. “You would use the same ideas.”
The idea is to create structures that can be stored and transported flat but popped into three-dimensional life when it’s time to use them.
Maria Redoutey, one of the doctoral students in his lab, is working on the problem of how switching structures from one shape to another might happen practically in the field.
“Now I can move the structure to any point along the path,” she said, demonstrating spring supports. “For the most part, I’m having to apply a much smaller force now, and it’s staying where I put it. So you can imagine how that would be good for like a big deployable bridge.”
Others students are actually working on deployable bridges and on folding boats and collapsible traffic cones and woven roofs and further applications for the production process used to make microscale robots.
Filipov’s work on the tiny machines was funded by the Defense Advanced Research Projects Agency, better known as DARPA, the organization at least partly responsible for the existence of the Internet, GPS technology and self-driving cars.
There are still problems to be worked out, largely related to integrating power sources into the machines, said Kenn Oldham, a mechanical engineering professor at U-M who works on the dynamics and control of microsystems and a collaborator on the project.
“A battery can’t necessarily be fabricated in the same process as the rest of it,” he said.
But most microrobots are prohibitively expensive and being able to start with a flat wafer of materials that then bend and shape themselves into “as much of the complete robot or system as possible…helps bring you towards more useful technology.”
Filipov sees the prospect of one day manufacturing them “in the hundreds of thousands.”
“So if you want to spatially monitor things, this would be a very effective way to do it, so for sensing, for inspection, of course, militaries are interested in the use for surveillance and things like that,” he said.
He envisions them someday – “and this is maybe 20, maybe 50 years from now” – working together like swarms of bees.
“If we can really look at that scale of what bees are able to do, you’ve got about 40,000 to 80,000 bees in a colony. They interact. They work together. They bring material out from the field, and they bring it in together, assemble it, make it into their house, make the food,” he said. “It would be really nice if we can actually get hundreds of thousands of these robots to work together to do something bigger.”
___
© 2022 Advance Local Media LLC
Distributed by Tribune Content Agency, LLC.