The recent unveiling of an entire barracks building 3D-printed with concrete showed off the latest example of the U.S. military putting additive manufacturing to work. But at least one expert says the Pentagon is still too wary of the new techniques.
On Monday, the Texas Military Department, which comprises the Texas Army and Air National Guard, cut the ribbon on a 3,800-square-foot barracks that will house 72 soldiers or airmen at the Camp Swift Training Center in Bastrop, Texas.
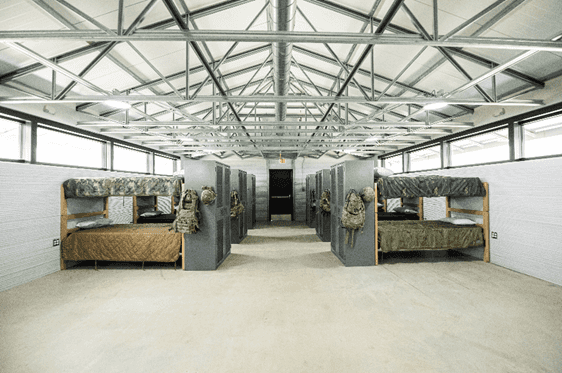
Even with the rapid advancement of 3D printing in recent years, creating an entire building of concrete in Texas presented unique challenges, said Evan Loomis, co-founder of ICON, the company that did the work. ICON has also worked on projects for the Air Force’s AFWERX and the Defense Innovation Unit, or DIU.
For instance, Loomis said, concrete behaves differently depending on the temperature, which is much less of an issue during conventional construction processes. Also, the firm had to ruggedize an enormous house-building robot to withstand the Texas elements.
Perhaps most importantly, he says, every building project produces valuable data that will make future builds easier. “Every time we are able to 3D-print a building, like the barracks, we are able to capture gigabytes of data about the weather that day, each layer, about pretty much everything you can imagine. After the moment where we are able to 3D print something for the first time we can take those learnings and develop algorithms that allow us to go better, cheaper, faster.”
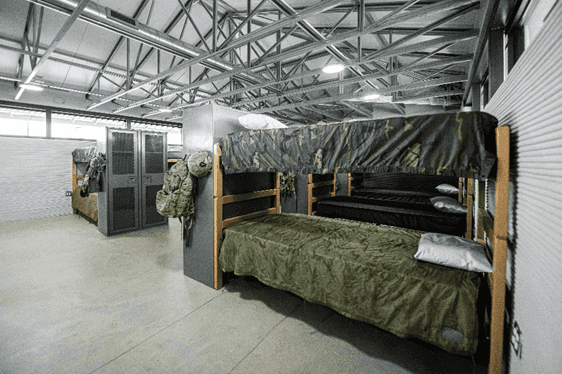
For instance, last year, the company was hired by DIU and the U.S. Marine Corps unit at Camp Pendleton in California, to train Marines to rapidly print structures in places where it’s hard to send materials or other supplies.
That’s one of the key areas of interest for the military in 3D printing, said Loomis. Typical structures “take a lot of types of building material, which complicates the supply chain” said Loomis. “ICON is using one material, concrete, that is readily available all over the world because it’s just sand, rocks and cement. People down range, simplifying the supply chain and custody of the material is a huge concern for them.”
The military is quickly embracing 3D printing, said Larry Holmes, a former DOD researcher in additive manufacturing who is now a professor at the University of Delaware. He says that as younger officers have risen to more important positions, he’s encountering more commanders that are already more comfortable with the new technology.
The military, and particularly the Army, is also beginning to embrace a new approach to writing requirements, with a much greater emphasis on whether or not the thing being contracted for simply performs the way that it’s supposed to. So-called performance based requirements are a change from the much more rigid design requirements that can lock the military into designs that are obsolete by the time they are deployed.
The United States leads the world on using 3D printing for highly advanced projects, like printing not only the bodies of aircraft like drones but increasingly the circuits as well, said Holmes. That has a lot of relevance for the special operations community.
“Those are the folks that are really excited about those, say, mission-specific drones. I mean, these things are”attritable, [cost] less than $2,000, [take] less than a day to print. You know, you have 24 hours to define your mission set, your mission parameters. As soon as you are ready to do that, you hit ‘print’ on this thing and you have your robot, drone, whatever it is.”
Increasingly, 3D printing is changing manufacturing and design below the level of DOD policy. It plays a role in everything from the various pieces of the Boeing 777 tanker aircraft to the Draco engines that SpaceX uses to fly space missions.
But while the United States is ahead technologically on 3D printing, Russia and China are putting it to wider use, said Holmes, noting that those countries have facilities to 3D print key components in hypersonic rockets and missiles.
“I think the reason why China and Russia have hypersonic manufacturing facilities and we don’t is because they’re willing to risk more than we are,” he said.
The key, he says, is taking the small risks now to keep the U.S. advantage.
___
© 2021 Government Executive Media Group LLC
Distributed by Tribune Content Agency, LLC.